AirBoss manufacturing engineer Dakota Reeves appreciates the importance of cost-effective, efficient processes.
He also understands that modern product development involves plenty of collaboration.
“There’s definitely a lot of communication between the product engineers and us as a manufacturing team,” he says of the back-and-forth between product development and manufacturing at AirBoss Flexible Products in Auburn Hills, Michigan. “You can come up with the best design in the world, but if you can’t manufacture it, it’s not going to do us any good.”
Dakota joined the AirBoss team in October 2020, and he brought with him an enthusiasm for the hands-on type of manufacturing process the company celebrates.
“I’m on the floor. I’m turning bolts and troubleshooting. As an engineer, I wanted to go the route of hands-on rather than sitting behind a computer.”
Dakota got his engineering education at Kettering University in Flint, Michigan. It’s there that he learned to balance advanced mechanical processes with enterprise-level manufacturing applications. He brought those skills with him into his first out-of-college job with Stellantis (formerly Fiat Chrysler), spending most of his days behind a desk. It was good work, but he itched for more on-the-manufacturing-floor immersion.
Amid layoffs and COVID uncertainty, Dakota found himself without a job and searching. He heard about a local company that valued its workers and was always looking for quality engineers, so he sent his resume to AirBoss of America.
“It’s a perfect fit for me,” he says. “I get to dive right in. I’ve got great teammates. The transition has been as smooth as I could have hoped for.”
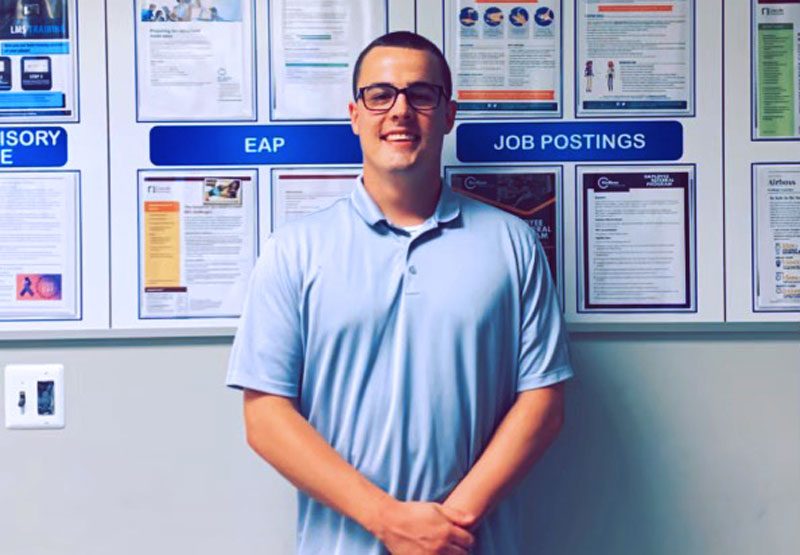
Dakota explains that since he’s new to the rubber industry, being able to bounce ideas off co-workers and mentors with decades of skin in the game is invaluable. He never feels boxed in or stuck, and it’s AirBoss’s open-door policy that’s made him comfortable learning from those with more knowledge and experience in the industry.
“Rubber as its own entity is a beast. There are a lot of outside factors, a lot of parameters, and a lot of things that people wouldn’t realize goes into rubber molding,” Dakota admits. “What really helped me transition was the teammates and leadership. We all have the same end goal, which is to produce the best quality parts hopefully as fast and efficiently as we can.”
Dakota calls out VP of Engineering Jeff Auten and Manufacturing Engineering Manager, Robert Angeles, specifically, in helping make his time at AirBoss rewarding and enjoyable.
“I spend a lot of time with [Jeff]. He’s always willing and excited to help. Instead of getting an eye roll, you get excitement, which is a good feeling as an engineer trying to learn as much as you can as quickly as you can.”
“My direct boss, [Robert], has been a huge help for me, too. He has around twenty-five years in the rubber industry. He knows the ins and outs, so anytime I get stumped I can go right to him to point me in the right direction.”
Dakota appreciates the collaborative nature of his work at AirBoss, and it’s the freedom to contribute that keeps him excited about the job.
“Sometimes, with corporations, you can get boxed into a cookie cutter type of role where they feed you the same work day in and day out,” he explains. “Here at AirBoss, there are no limitations to what project you can work on. You’re not boxed in. If I want to help a design engineer with a design, they’re more than happy to let me do that. They’re very receptive.”
When Dakota isn’t helping keep the manufacturing floor operating smoothly, you can catch him outside of work “watching all of the sports games” and spending valuable relaxation time with his family.