Table of Contents
According to AirBoss Engineered Product’s VP of Engineering, Jeff Auten, it’s the ability to work with customer challenges – paired with talent and state-of-the-art technology – that is one of the main factors which keeps the company competitive.
“What’s unique here is the combination of compounding from the AirBoss side and the molding and manufacturing experience,” he says. “On the engineering side, we’ve added strength to the team to help with the design of more complex parts.”
As a result, AirBoss can provide quotes on products they weren’t able to even as recently as a few years ago. For Auten and his team, that’s a win by any definition.
Hydraulic Mount R&D a Good Example of Innovative Product Testing
At AirBoss, it’s par for the course to work closely with a number of clients to conceive, design, prototype, test, and manufacture parts and custom compounds.
Often, an innovative approach to a complex challenge leads to a completely new product, and even if concepts that only reach certain stages of design or production still result in new valuable insights and knowledge.
Since early 2021, AirBoss Engineered Products (AEP) has worked with a handful of companies to test new product implementations, namely, rubber-molded hydraulic mounts meant to replace traditional pure rubber mounts in certain applications.
“Conventional mounts, where they’re just completely made of rubber, are very simple,” explains Auten. “The only damping that you can expect is from the rubber material itself, which is limiting.”
“A hydraulic mount is a rubber-to-metal molded part that, in the assembly, includes a hydraulic fluid much like a shock absorber in a vehicle does,” Auten continues. “We’re able to push fluid through internal chambers inside the rubber hydraulic mount, and that acts as a damping mechanism.” Simply put, hydraulic mounts are better at precision damping, which means they’re better suited for some clients’ needs.
Auten understands that it’s AirBoss’s ability to create advanced products that sets the company apart from the competition.
“We’ve been recognized by our customers as being a potential supplier for these types of mounts. There are a lot of companies around the world that can produce rubber-to-metal parts,” he admits, “but a lot of them don’t harness the engineering to make the hydraulic mounts.”

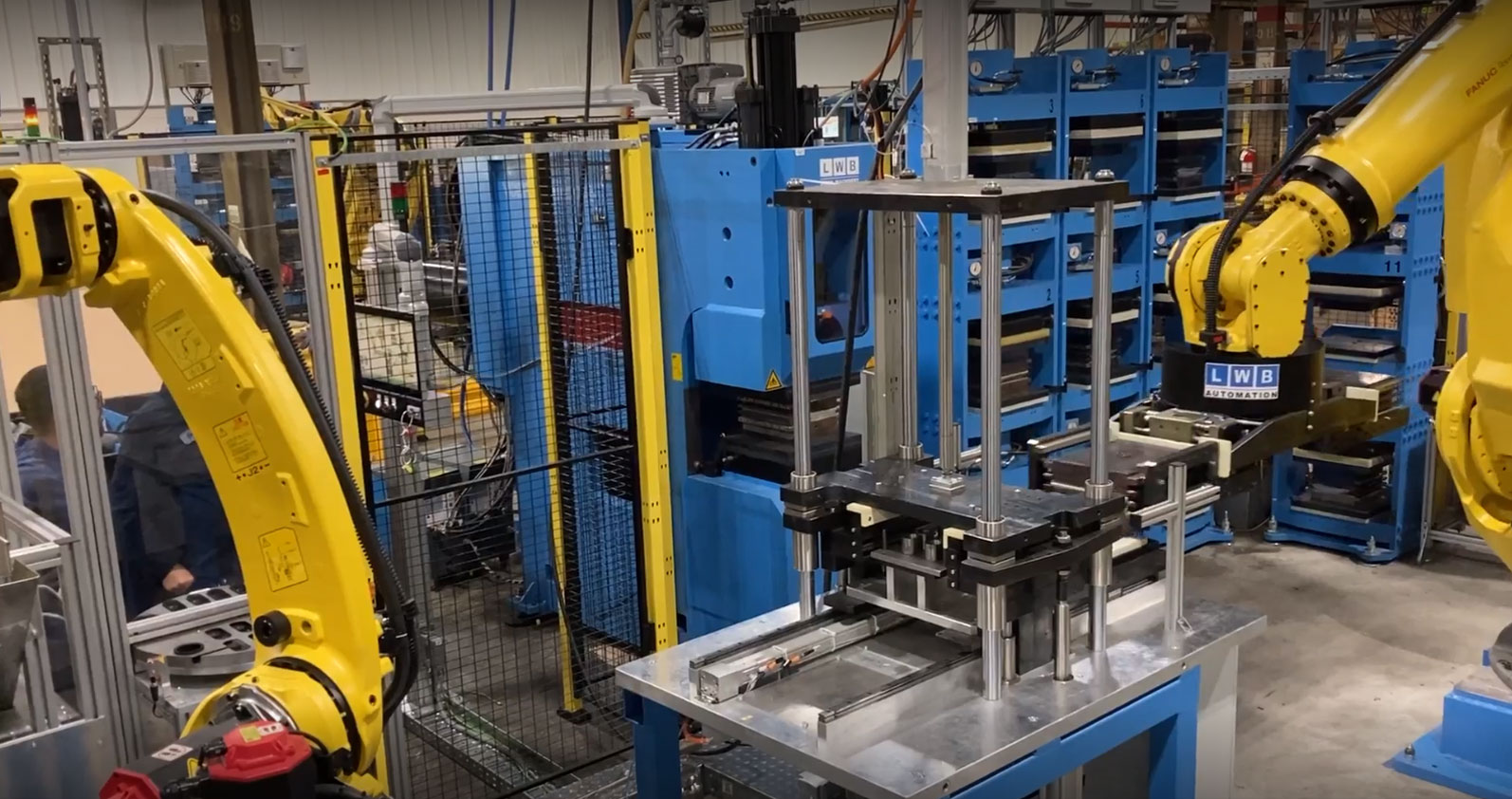
Advanced Product Innovation is the Name of the Game for AEP
Branching out, tackling new projects, and improving processes continues to be a winning strategy for AirBoss. AirBoss and AEP are constantly looking for new ways to innovate rather than stay complacent and only sell a handful of legacy products. In fact, product innovation is what drives Auten and his team to stay creative.
“When I joined AirBoss three years ago, that was my technical commitment – to increase the know-how of certain high value-added engineered parts,” he says. In essence, it was his job to think of ways the company could improve processes, products, and people’s way of thinking to include more advanced solutions to traditional challenges.
Fortunately, in the enterprise-level manufacturing world, everything is connected, and Auten and his team understand that each piece of the puzzle informs, improves, and elevates the next.
“You incorporate the design engineering, and then you carry that into the manufacturing engineering where we’re using our robotic auto cells,” Auten says. “I’d say we have a pretty state-of-the-art solution for some customers.”
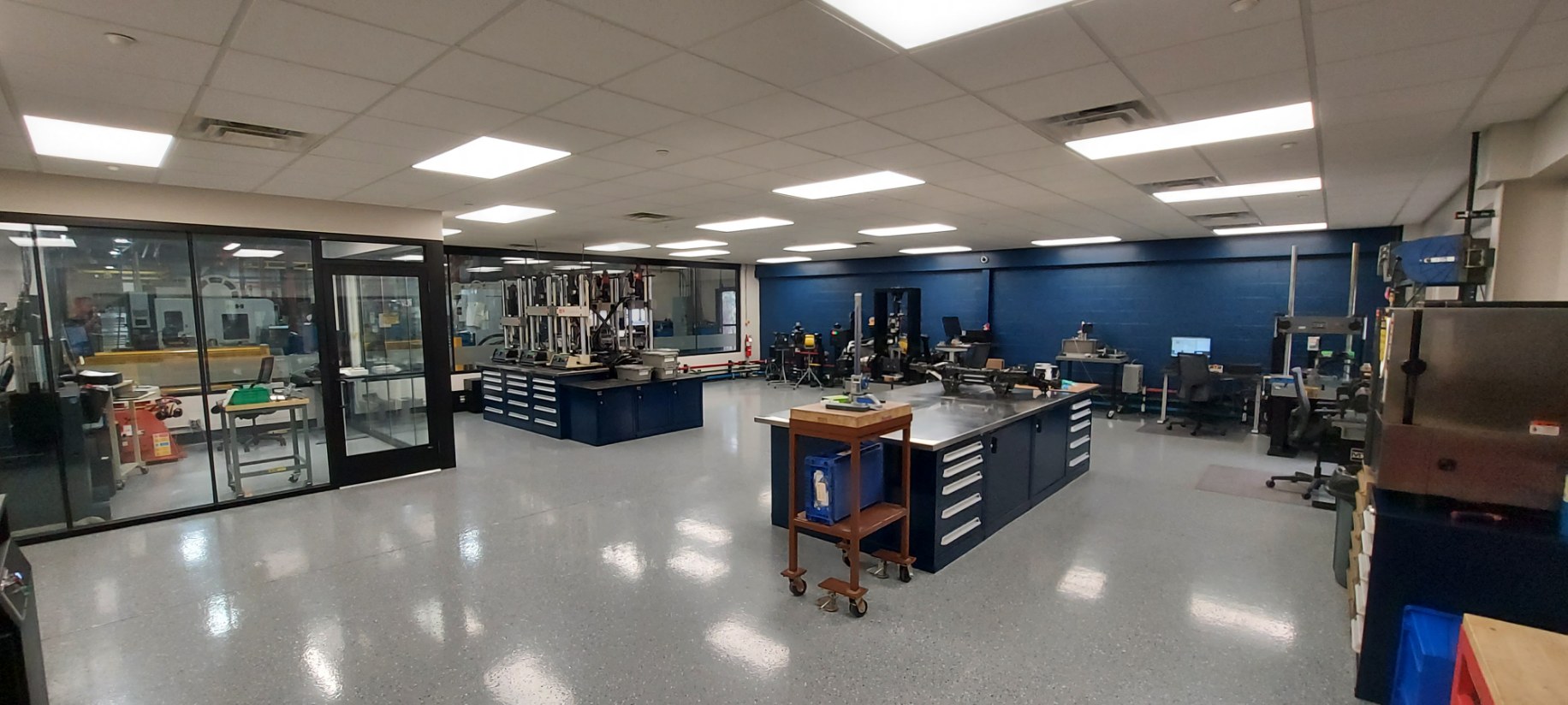
Solutions, Improvements, and Innovations Never End at AirBoss
Auten is quick to point out that past innovations often lead to new opportunities. Launching the HydroBoss™ showed other companies that AirBoss can produce a more advanced mount, and clients got curious.
“We’ve had this company for a long time, and they never recognized us as a hydraulic mount supplier,” he says, “but after we launched Lucid, they came to us and asked us to design and quote a hydraulic bushing mount that could potentially replace what they had.”
Auten chalks up AirBoss’s competitive qualities to the company’s ability to combine its rubber compounding – which AirBoss has been perfecting for decades – with rubber molding know-how and an ever-growing team of experienced, energized material engineers.
Assembling all the pieces in a way that’s beneficial to new and existing clients is something AirBoss does very well.
“Putting the basic building blocks out there helps open doors to other areas,” Auten says with candor.